As the exclusive New England affiliate of Christie’s International Real Estate, as well as the largest manager of commercial forestland in the Northeast, LandVest has a unique perspective on the timberland and housing lifecycle. From my present perch, the spring home construction market has me tariffied.
We build houses out of wood. Specifically, the largest component of home construction is softwood lumber. Framing and decking, shingles and plywood, mouldings and doors, all rely on coniferous trees. Most consumers don’t realize that the majority of softwood logs harvested in Northern New England states like Maine, New Hampshire, Vermont and New York, get shipped to Canada for processing. After being sawn into lumber, many of these building materials are shipped back to the US.
Available: 92 Spruce Harbor Trail | Stonington, ME | $4,875,000
The United States has had a complicated, but symbiotic relationship with Canadian lumber over the past 50 years. The US relies on Canada for about 1/3rd of its softwood lumber needs. So while we have always imposed anti-dumping penalties and countervailing duties on cheaper Canadian lumber, we have been wise to set those duties at a level bar to encourage import volumes at equitable rates to meet our demand.
Disrupting the regulated flow of Canadian lumber will be devastating on our housing production. In the early days of COVID-19, U.S. manufacturers idled about 30% of American capacity, expecting a slowdown in demand. When demand never waned, lumber prices skyrocketed, driving softwood lumber prices to almost 3x their prior historic high. It took almost three years for supply chains to recover.
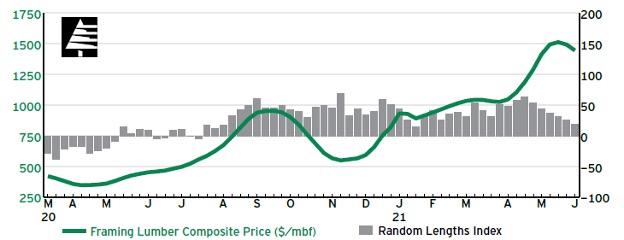
We are now at the same precipice, just as the spring building market is upon us. A 25% tariff on top of the nearly 15% countervailing and anti-dumping duties already imposed on Canadian lumber would make it uneconomical to import into the US. This would, in turn, halt the purchase of all US logs flowing into Canada, shutting down timber harvest in border states, and negatively affecting employment.
Based on the lessons of 2021, we can expect to see lumber prices skyrocket, when 1/3 of domestic supply is cut off. Admittedly, US softwood lumber manufacturers will benefit from higher lumber prices (while the US consumer suffers). Ironically, however, the 2nd, 4th and 6th largest producers of softwood lumber in the United States are the Canadian companies, West Fraser, Interfor and Canfor.
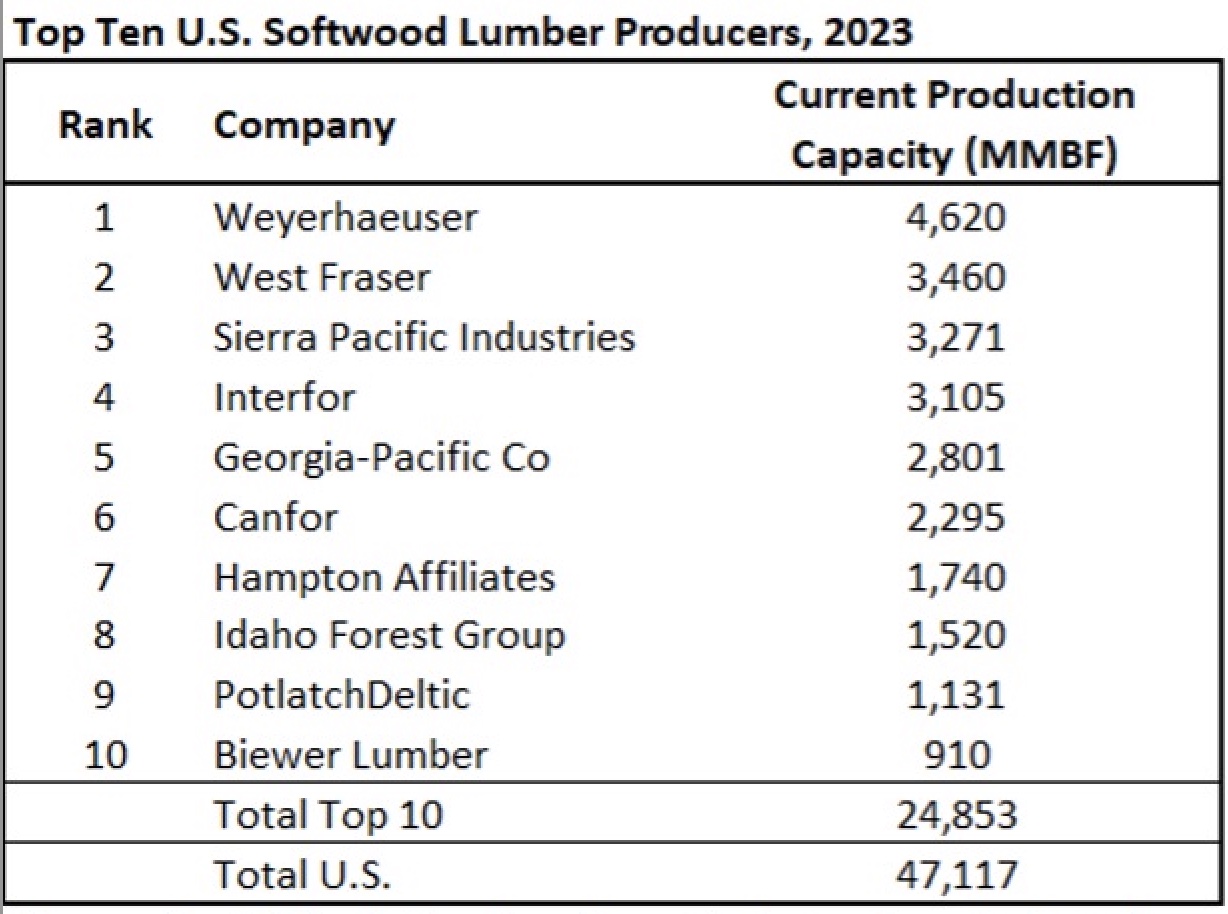
Higher construction costs, in the face of increased borrowing rates, will stifle spring construction, at a critical time when we have underbuilt the US housing stock by 8.5 million units (read my previous blog about the underbuilt housing market).
Tension remains in the residential housing market. While this is a bleak message for many trying to penetrate the American dream of home ownership, it prolongs a strong seller’s market for current home sellers – especially those in the luxury space.